Non-destructive testing (NDT) covers a diverse range of techniques designed for assessing the integrity of materials, most typically metals. Applications include evaluating compliance of fabricated items with material specifications and identifying degradation which can occur during the service life of equipment or structures.
Radiography
Radiography is the most commonly known non-destructive test method. It can be used to obtain permanent image of surface and sub-surface (embedded) discontinuities. The same discontinuities can be radiographed again after a period of service life and the radiographs can be compared to measure the change in the size and shape of the discontinuity.
Some of the common uses are detection of surface and subsurface features of interest in welded parts, castings, forgings, wall thickness measurement, corrosion mapping, detection of blockages inside sealed equipment, detection of reinforcing material in concrete slabs, measuring bulk density of materials, measuring porosity in concrete, etc.
We can provide equipment and personnel to carry out X-ray and Gamma test techniques for the testing of welds, castings and forgings in both ferrous and non-ferrous materials. MIS has two radiographic exposure bays that enable us to carry out radiography at our premises.This allows clients to deliver items to us where we aim to provide a 24hr service. With no call out of technicians this can be a quicker and cost effective service for clients.
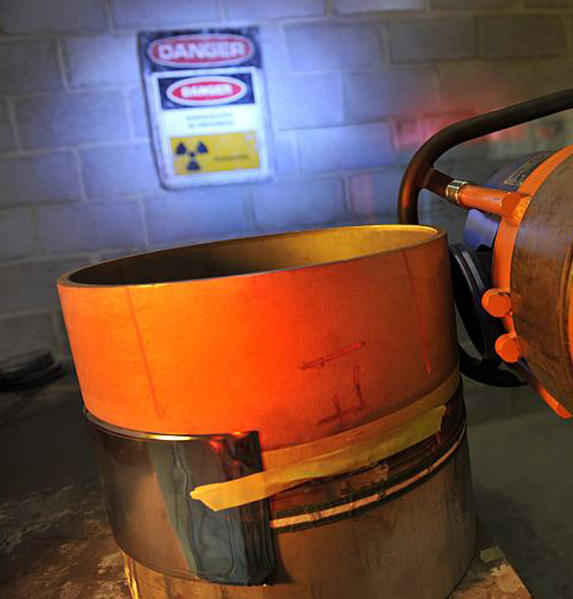
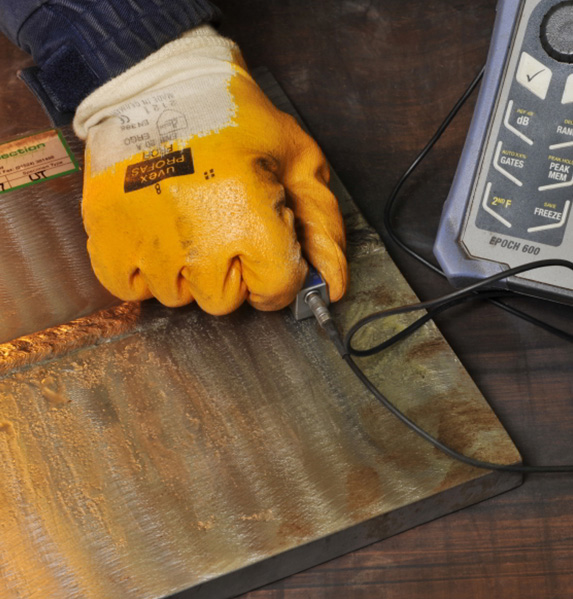
Ultrasonic Inspection
Ultrasonic Inspection is very sensitive test method for detection of embedded linear discontinuities. Ultrasonic testing is faster and economical as compared to radiographic examination.
The common applications of ultrasonic testing are wall thickness measurement, corrosion mapping, lamination testing , flaw (discontinuities) detection in the material e.g. welds, castings, forgings and other wrought products, density measurement of material, hardness measurement, etc.
We can provide equipment and personnel to carry out ultrasonic testing on a wide range of weld configurations and materials.
- Welds, plate, pipe, beams, T joints, TKY joints
- Castings, forgings, metal bearing bonds.
- Lamination checks, plate scans, full floor scans, prepped joints prior to welding.
- Thickness testing, ship hull surveys, tank inspection.
Magnetic Particle Inspection
Magnetic Particle Inspection (MPI) is very sensitive test method. It can detect tight in-service fatigue cracks in rotating parts or creep cracks on steam piping. Magnetic Particle Inspection cannot be used for non-ferrous materials and non-magnetic ferrous materials such as austenitic stainless steels.
The test method involves application of magnetic field externally or applying electric current through the material which in turn produces magnetic flux in the material. Simultaneously, visible ferrous particles on sprinkled or sprayed on the test surface. The presence of a surface or near surface discontinuities in the material causes distortion in the magnetic flux which in turn causes leakage of the magnetic fields at the discontinuity. The magnetic particles are attracted by the surface field in the area of the discontinuity and adhere to the edges of the discontinuity appearing the shape of the discontinuity.
Testing methods used include, fluorescent particle, black on white, chlorine free fluorescent and dry powder for hot root examination.
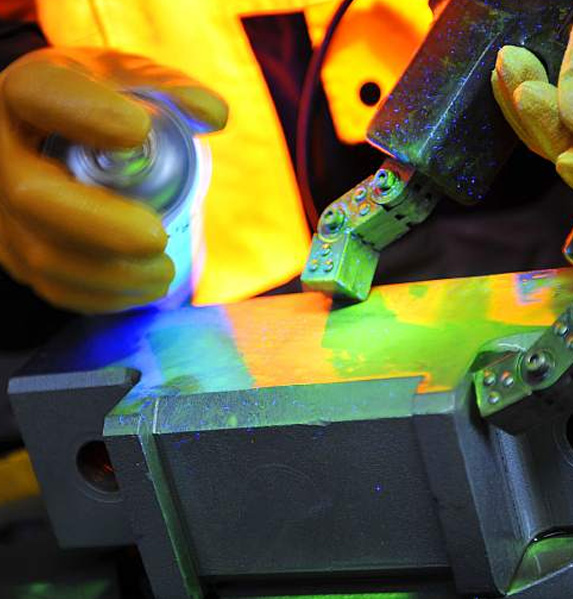
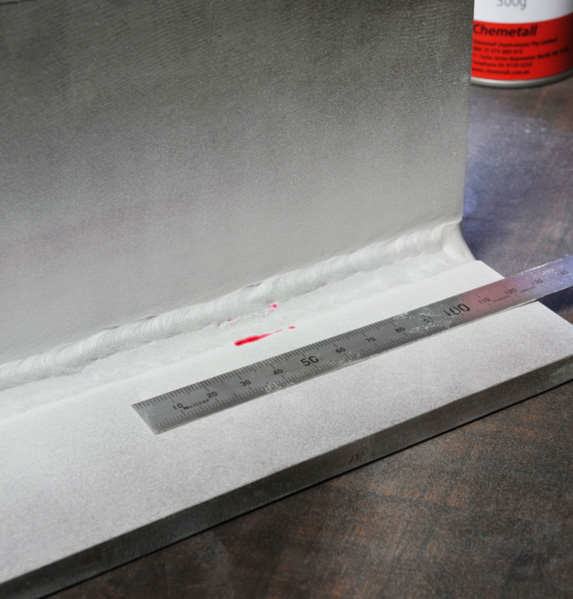
Dye Penetrant Inspection
Dye Penetrant Inspection (DPI) also called as Liquid Penetrant Inspection (LPI) is fast, economical and widely used non destructive test method to detect surface-breaking discontinuities in all non-porous materials (metals, plastics, or ceramics).
Penetrant test is performed by cleaning the test surface thoroughly, applying coloured or fluorescent penetrant, allowing penetration time, removal of excess penetrant followed by application of developer ( dry or liquid form). The developer assists to draw penetrant out from the surface breaking discontinuities.
After developer dwelling the test surface is examined for bleed out under natural light or black (UV) light.
Other NDT Services
- Vacuum Box Testing
- Leak Testing
- 3rd Party Witnessing
- Portable Hardness
- Positive Material Identification
- Ferrite Testing
- Holiday Testing
- Visual Inspection
- Welder/Welder Procedure Certification
- Level III NDT Consultation
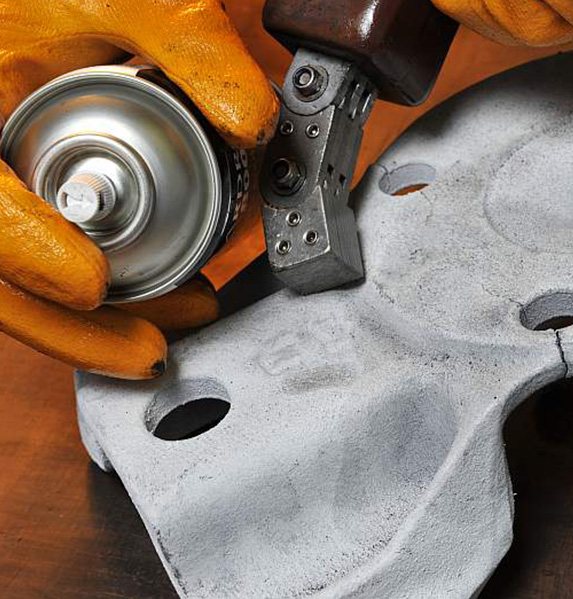